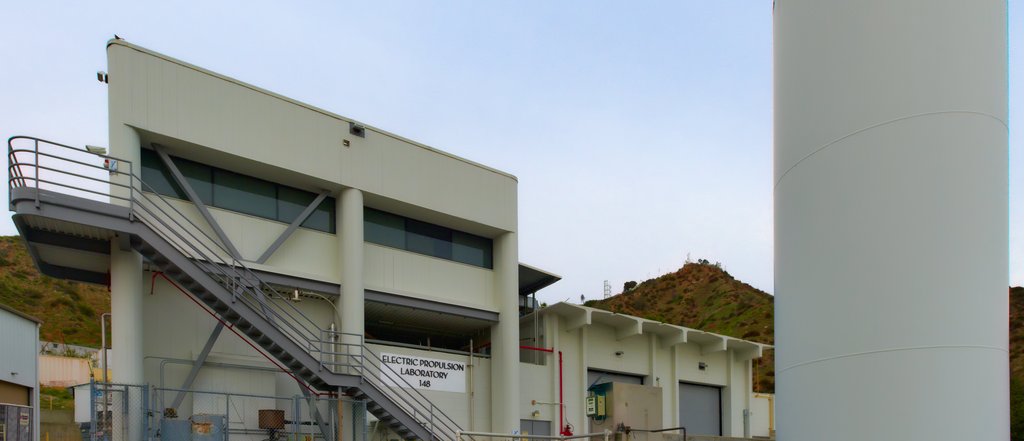
Facilities
The Electric Propulsion (EP) laboratory at JPL maintains several vacuum facilities for evaluating the operation, performance, lifetime, and integration of electric thrusters and related technologies on deep-space missions. Chambers range in size from small bell jars to the large 3 m diameter by 10 m long Owens Test Facility used for high-power EP thruster testing. Most chambers are cryopumped with sufficient pumping speed to handle flow rates typical of electric thrusters. Thermal vacuum testing in several facilities is available for testing from temperatures less than -120°C to over +450°C.
Random vibration and shock testing are also available using other facilities at JPL. All thruster test facilities are highly instrumented with robust high- and low-speed thruster telemetry as well as other diagnostics including thrust stands and an assortment of state-of-the-art optical- and probe-based systems for measuring plasma properties.
Test facilities are equipped with on-site machine tools, 3D printing, and fabrication equipment for support of test activities. There is significant electrical power and liquid nitrogen infrastructure for facility operation. A wide range of power supplies (> kilovolt and >kiloamp capabilities), electrical diagnostic equipment, IP and high-speed cameras, and data acquisition systems are available. Most facilities are setup to safely operate unattended for long duration tests. A 420 sq. ft., class 10,000 clean room is available for test and flight hardware. Our facilities and personnel are available to support development activities in government, academia, and industry. The primary facilities are described below. Contact the EP group supervisor for further details.
Owens Test Facility
The Owens Test Facility is a 3 m diameter by 10 m long vacuum chamber used previously for the 30 kh life test of the 2.3 kW NSTAR ion thruster, various flight qualification TVAC efforts, magnetically shielded Hall thruster development, and has also been used to test Hall thrusters and Ion thrusters at power levels up to 20 kW. The facility is cryogenically and turbo-molecularly pumped and is lined with graphite panels to minimize backsputtered material to thruster surfaces. Base pressures as low as 10-8 torr are routinely achieved and the measured pumping speed of the facility on xenon is 400 kl/s. A high-resolution thrust stand is available for measurements over 0.001 - 1 N. Additionally, arrays of plasma probes and optical diagnostics (infrared camera, high-speed visible camera, and laser induced fluorescence) are available for interrogating the interior and plume regions of thrusters. Flight-like harnessing, thruster high-speed telemetry, and robust Ground Support Equipment (GSE)/thruster protection systems are in place to support the Advanced Electric Propulsion System 12 kW Hall thruster development programs for the Power and Propulsion Element as part of NASA’s Lunar Gateway.
Highbay Test Facility
The High-Bay test facility is 2.6 m diameter and 5.2 m long with six cryogenic pumps (four sails and two charcoal arrays) that operate in parallel with a turbomolecular pump to generate a nominal pumping speed of 200 kl/s on xenon. All internal surfaces of the chamber with line-of-sight to the thruster’s discharge channel are covered with either graphite panels or graphite foil. The facility is equipped with a thrust stand, full suite of thruster instrumentation (slow and high-speed) and DAQ systems, quartz crystal microbalance (QCM), rotationally swept plasma diagnostics package, and more. Interlocks and failsafe systems enable extended unattended operation of thrusters in the facility for life qualification testing such as the 100 kg-Xe throughput life demonstration of the 1 kW ASTRAEUS thruster that was performed in the facility.
Component Test Facility
The Component Test Facility is a dedicated facility for flight qualification TVAC cycling of thruster components (magnet coils, heaters, RTDs, etc). This 1.5 m diameter 2.5 m long facility is supported by cryogenic and turbomolecular pumping and has a multitude of DC power supplies for heating up to 11 independent test fixtures along with discrete LN2 supply valving for each fixture. Various failsafes and interlocks along with numerous instrumented sensors and software control enable safe unattended cycling of qualification hardware components.
Microthrust Propulsion Laboratory
The Microthrust Propulsion Laboratory (MPL) is a Class 100, 1000 sq. ft. cleanroom equipped with services and workstations for multiple projects. The facility features a 2 m diameter, 2 m long ultra-high vacuum (UHV) test chamber with multiple beam targets, a rotational and translational positioning system to adequately assess microthruster performance at <10-8 Torr, neutralizer integration, lifetime, and potential spacecraft integration and contamination issues. The MPL cleanroom includes three other vacuum chambers for thruster testing. Thruster diagnostics in the vacuum chambers include micronewton thrust stands, Faraday probes, beam targets, time-of-flight and Temperature-Controlled Quartz Crystal Microbalances (TQCMs). The facility also includes 1 micron particulate cleaning equipment for thruster and propellant feed system components, a 3-axis micron precision thruster component alignment measurement microscope and a Scanning Electron Microscope (SEM) with energy dispersive x-ray spectroscopy (SEM/EDS) for nanometer scale thruster component inspection, contamination and failure analysis.
Condensable Metal Propellant Vacuum Facility
The Condensable Metal Propellant Vacuum Facility is a unique national asset for developing high-power, liquid-metal fueled propulsion systems. It is the only large-volume vacuum facility in the nation capable of testing high-power (MW-class), liquid-metal fueled thrusters and is equipped with water-cooled shrouds providing up to 2.5 MW cooling/pumping capacity. Steady-state power up to 1.0 MW is presently available. The chamber measures 3 m diameter by 8 m long. Light gases are pumped with diffusion pumps with a pumping speed of 74,000 l/s on air.
Cathode Testing Facilities
A dedicated lab area houses 4 vacuum chambers used for cathode discharge testing and qualification life and TVAC testing. Each chamber is cryogenically pumped and the larger facility has demonstrated LaB6 cathode discharge operation up to 500 A.
Cathode Diagnostics Test Facility
The Cathode Diagnostics Test Facility is a 1 m diameter 2 m long vacuum facility pumped by two 25 cm diameter cryopumps with base pressures typically of 3x10-7 torr-Xe. This facility is highly instrumented with various optical- and probe-based diagnostics, including a unique optical pyrometry diagnostic for measuring the insert temperature of hollow cathodes during operation. The facility also employs a Hall thruster cathode simulator to setup the proper magnetic fields as well as discharge current oscillations that exist when operated with a full Hall thruster.
National Direct-Drive Testbed
The National Direct-Drive Testbed array of 57 solar panels mounted above the EP laboratory has enabled the ground test operation of Hall thrusters up to 12 kW of peak power. The direct-drive powering of EP thruster—that is direct copper lines from solar panels to thruster—differs from the conventional use of bulky, heavy, complex, and costly power processing units (PPUs) used in tradition ground and flight EP thruster operation. This unique capability enables JPL ground testing of novel direct-drive systems that offer tremendous potential mass and cost savings for high-power EP missions. Direct-drive testing to date with the H6 from power levels of 1-10kW, has demonstrated stable operation nearly identical to regulated DC laboratory power supplies with discretized but otherwise identical throttleable ranges.
CL#24-0850